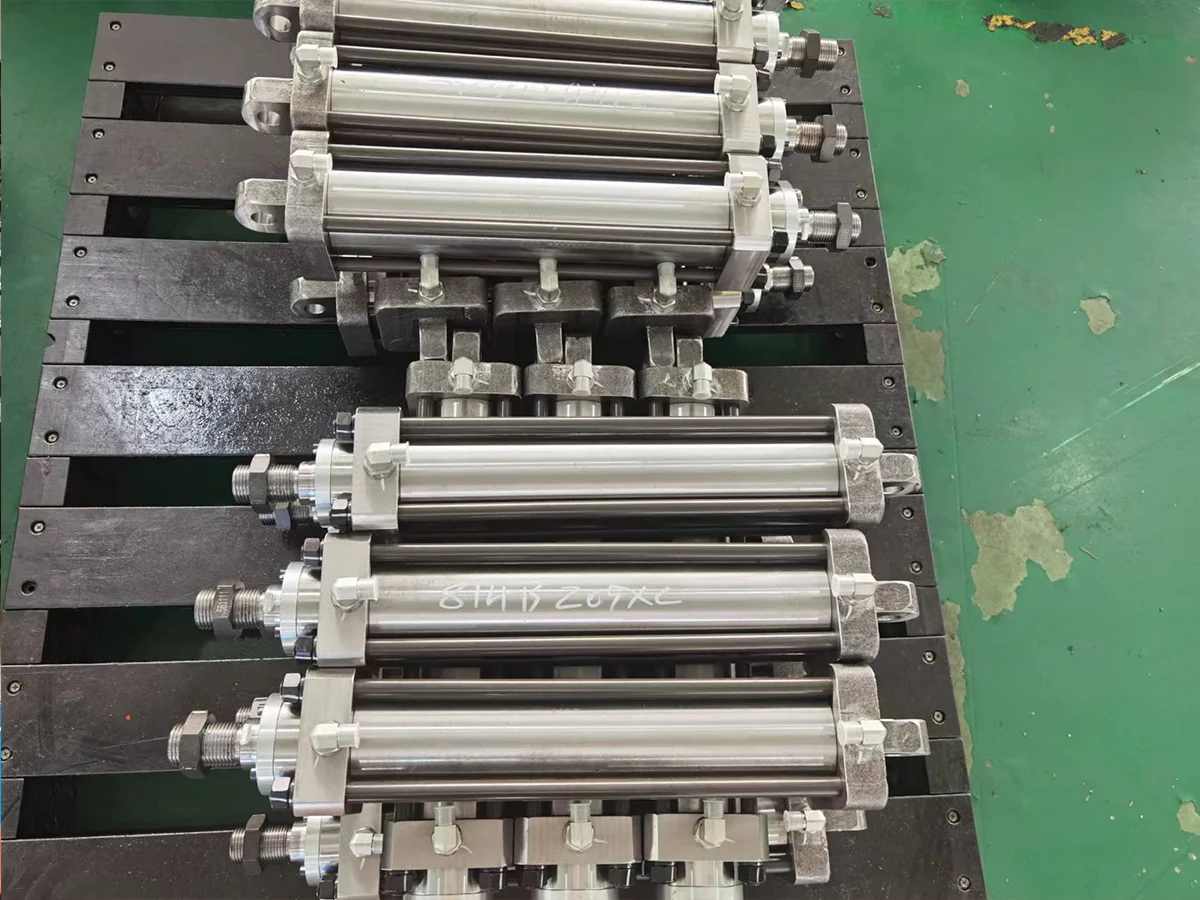
Hydraulic cylinders are important and indispensable actuators in hydraulic systems and are widely used in various industries such as engineering machinery, metallurgical equipment, mining machinery, agricultural machinery, etc. Welded hydraulic cylinders are particularly suitable for high pressure and large load applications due to their compact structure, high strength and excellent sealing performance. However, the working environment of hydraulic cylinders is usually harsh, such as outdoor operations, high humidity, muddy water, acidic and alkaline media, salt spray, etc., which may cause the hydraulic cylinder to rust or corrode. Once the welded hydraulic cylinder is rusted, it will not only affect the appearance, but more importantly, it will reduce the strength, damage the seal, affect the stroke and even cause failure. Therefore, how to prevent the welded hydraulic cylinder from rusting or corroding is an important topic to ensure its long-term reliable operation.
This article will explain in detail how to effectively prevent the welded hydraulic cylinder from rusting or corroding from the aspects of corrosion principle, influencing factors, protective measures, daily maintenance, etc.
1. Causes of rust and corrosion of welded hydraulic cylinders
Before understanding the protective measures, we need to know why the hydraulic cylinder rusts or corrodes. The main reasons include:
Material problems
The main components of hydraulic cylinders, such as cylinder barrels and piston rods, are usually made of carbon steel or alloy steel. If the surface treatment is not done well, these steels are prone to oxidation reactions and generate rust layers when they encounter moisture, oxygen, acid, alkali or salt.
Harsh working environment
Welded hydraulic cylinders are often exposed to high humidity, rain, mud, sea breeze (including salt spray), chemicals and other environments, all of which may accelerate their corrosion.
Surface protection failure
Hydraulic cylinders are generally treated with protection such as painting, electroplating, phosphating, and chrome plating during production. If the surface protection layer falls off due to scratches, impacts or aging, the exposed metal parts will soon rust.
Seal failure
The hydraulic oil inside the hydraulic cylinder itself has a certain anti-rust effect, but if the seal is poor, the oil is contaminated or leaks, it may also cause the internal parts to rust.
2. Main measures for rust and corrosion prevention
To effectively prevent rust or corrosion of welded hydraulic cylinders, corresponding measures need to be taken in various links such as design, manufacturing, installation, use and maintenance.
2.1 Material selection and surface treatment
Select corrosion-resistant materials
For parts that may come into contact with corrosive media, materials with better corrosion resistance such as alloy steel and stainless steel can be selected.
Surface protection treatment
The cylinder barrel and piston rod can be chrome-plated to improve the surface hardness and corrosion resistance.
Sandblasting, primer + anti-corrosion paint treatment are performed on the welding parts and the overall shell.
Nickel plating, zinc plating, phosphating and other processes can be used to increase corrosion resistance.
For hydraulic cylinders that are exposed to salt spray for a long time, special coatings or protective films can be used.
2.2 Reasonable design
Try to reduce dead corners, grooves, and water accumulation areas to prevent rainwater and dirt from remaining.
The seal design should be reasonable to ensure that the internal oil does not leak and external moisture is not easy to penetrate.
The shell is equipped with drainage holes to prevent water accumulation inside.
2.3 Correct installation and protection
Avoid scratching the surface and damaging the coating during installation.
When using outdoors, try to add protective covers and rain shelters.
For marine climate or highly corrosive environment, dust cover and bellows can be installed to protect the piston rod.
2.4 Reasonable use
Use qualified hydraulic oil and replace it regularly. Hydraulic oil not only has a lubricating effect, but also prevents rust.
Avoid long-term parking in humid, muddy, and salt spray environments.
Do not overload or overpressure to avoid mechanical impact to damage the protective layer.
3. Daily maintenance points
Even if it is carefully protected at the factory, the hydraulic cylinder may still rust if it is not maintained daily. Therefore, it is very important to do a good job of daily maintenance.
Regular cleaning
Wipe the surface of the hydraulic cylinder and the piston rod with a clean soft cloth regularly to prevent sludge and sand accumulation, scratches and moisture absorption.
If there is acidic and alkaline dirt, it should be cleaned in time.
Apply anti-rust grease regularly
For the piston rod part, you can apply anti-rust oil, butter, etc. regularly, which is especially important during idle period.
Check the coating
Check whether there are cracks, peeling, and scratches on the surface paint, plating, and welds. Once found, they should be repaired in time.
Check the seal
Regularly check whether the seals are aging, cracking or leaking, and keep the inside free of water and air.
Idle storage
If the hydraulic cylinder is not used for a long time, it should be:
Lubricated piston rod and rust-proof grease;
Stored in a dry, ventilated place away from direct sunlight and rain;
The piston rod can be wrapped with plastic film or cloth bag to isolate the air.
4. Protection suggestions for special environments
Marine environment
The sea breeze contains a lot of salt, which corrodes steel very quickly. Therefore, high-performance nickel plating/chrome plating + anti-corrosion paint should be used for double protection, and stainless steel parts should be used.
Chemical environment
If there are strong acids, alkalis or corrosive gases in the working environment, corrosion-resistant materials should be selected and the protective coating should be thickened.
High temperature or high humidity environment
Coatings, seals and lubricants with good stability under high temperature and high humidity conditions should be selected to prevent high temperature oxidation or water vapor penetration.
As a high-strength and high-precision hydraulic actuator, the performance stability and life of the welded hydraulic cylinder not only depend on the manufacturing process, but also depend on scientific and reasonable anti-rust and anti-corrosion measures. Only by fully considering anti-corrosion factors in the process of material selection, design, manufacturing, installation and use, and insisting on daily maintenance, can we maximize the service life of hydraulic cylinders, reduce failure rates and improve work efficiency.
As a professional welding hydraulic cylinder factory, we are well aware that hydraulic cylinders are prone to rust and corrosion when exposed to outdoor, high humidity, salt spray and other environments for a long time. Therefore, in the design and manufacturing process, we strictly select high-quality corrosion-resistant materials, the cylinder body is made of high-strength steel and undergoes multiple surface protection treatments such as chrome plating and painting, and at the same time optimizes the structure to reduce dead corners of water accumulation. Before leaving the factory, it also undergoes strict salt spray testing and sealing testing to ensure superior anti-rust and anti-corrosion performance. We not only provide high-quality products, but also provide customers with professional protection suggestions and maintenance plans to help users use them with confidence in various harsh environments and extend the service life of equipment.
www.toringcylinder.com
toringcylinder