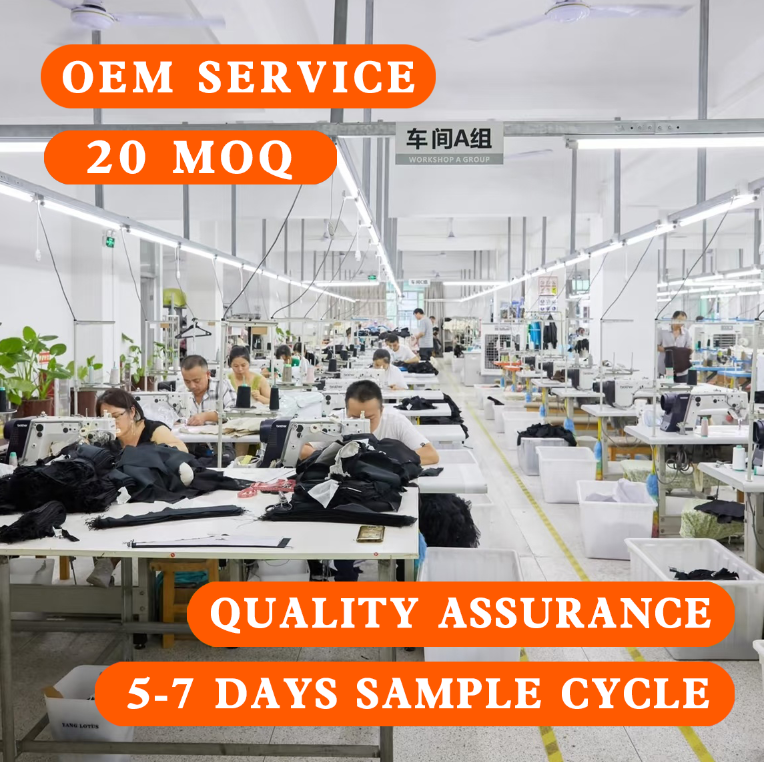
With the continuous development of the fashion industry, consumers have higher and higher demands for the design, quality and personalization of clothing. In order to meet the diversified needs of the market, more and more brands and entrepreneurs choose to cooperate with professional clothing manufacturers to turn their creativity into exquisite ready-made clothes. From the initial design concept to the final presentation on the shelf, a ready-made garment often needs to go through a rigorous process. Understanding the production process of clothing manufacturers not only helps brands control quality and optimize costs, but also improves the efficiency of communication with manufacturers.
1. Preliminary preparation: demand confirmation and communication
Before formal production, clothing manufacturers will fully communicate with customers. This step is called "demand confirmation", which mainly includes the following aspects:
Determine the design concept
Customers need to explain the design concept, target market, style positioning, color preference, fabric requirements, etc. to the manufacturer. Some brands already have complete design drawings, while some entrepreneurs may only provide reference styles or inspiration pictures. At this time, manufacturers usually provide design suggestions or help improve the design.
Choose fabrics and accessories
Fabrics and accessories are the soul of clothing, which directly affect the texture, comfort and cost of the finished product. Manufacturers usually display sample fabric cards and auxiliary material samples to allow customers to choose the appropriate fabrics, buttons, zippers, wires, etc.
Determine the production quantity and budget
The production quantity and budget also need to be agreed in advance. Different manufacturers have different minimum order quantities (MOQ). Customers need to negotiate a reasonable production scale with manufacturers based on their own market needs and budget.
2. Sample making stage: sample production
After completing the preliminary communication, the clothing manufacturer will start making samples according to the needs of the customer. This stage is also called "sample making" or "sample development".
Paper pattern design (pattern making)
The manufacturer's pattern maker will make paper patterns based on the design draft or sample clothes, which is a key link in clothing production. The paper pattern not only needs to meet the design effect, but also takes into account the fabric characteristics and human body structure.
Sample sewing
According to the paper pattern, the cloth pieces are cut out and sewn into sample clothes. Sample clothes are mainly used to verify the pattern, size, craftsmanship, fabric effect and overall appearance.
Sample confirmation
After receiving the sample clothes, the customer will try them on and check them, and make suggestions for modification. Usually, the sample needs to be modified 1-3 times until the customer confirms that it is correct before entering the mass production.
3. Fabric procurement and preparation
After the sample is confirmed, the manufacturer will start to purchase the required fabrics and accessories according to the order requirements. Excellent clothing manufacturers usually have a stable supply chain that can guarantee the quality and supply speed of raw materials.
Fabric acceptance
The purchased fabrics need to be inspected, including color, feel, weight, shrinkage, color fastness and other indicators to ensure that they meet production requirements.
Fabric pre-shrinkage and finishing
In order to avoid shrinkage or deformation of the finished product, the fabric is usually pre-shrinked and ironed to make it more stable.
4. Mass production: from cutting to sewing
Mass cutting
After the fabric is ready, the cutting worker will cut the fabric into garment pieces according to the confirmed paper pattern. Modern clothing manufacturers are usually equipped with automatic typesetting and laser cutting equipment, which not only improves efficiency but also reduces waste.
Sewing assembly
The cut garment pieces will be sent to the workshop and sewn by workers according to the process flow. Different types of clothing may require different sewing processes and special equipment, such as overlock machines, flat-sewing machines, and interlocking machines.
Intermediate inspection
During the production process, manufacturers usually set up quality inspection links to conduct random inspections on semi-finished products to ensure that the quality of each process meets the standards.
5. Post-production process: ironing, inspection, and packaging
After the sewing is completed, the clothing needs to go through a series of post-production processes before it can become a real finished garment.
Ironing
The newly finished clothes often have wrinkles or unevenness, and need to be sorted out by steam ironing and other methods to make the clothes flat and beautiful.
Quality inspection
The finished garments need to undergo strict quality inspections, including inspections of appearance, size, thread ends, stains, color differences, etc. Excellent manufacturers will conduct random inspections according to AQL standards.
Packaging
The clothing that passes the quality inspection will be packaged according to customer requirements, such as single-piece packaging, whole package, with hang tags, with size stickers, etc., and finally packed and packaged.
6. Delivery and after-sales
After the finished product is completed, the manufacturer will ship the goods according to the agreed time and method, and provide shipping documents. Some clothing manufacturers also provide certain after-sales services, such as returns, repairs, quality tracking, etc.
7. Advantages of the production process of clothing manufacturers
Through the above steps, it can be seen that there are many advantages to cooperating with professional clothing manufacturers:
Professional team support: From design to finished clothing, there is an experienced team to follow up.
Efficient production process: Systematic production process ensures timely delivery.
Quality assurance: A complete quality inspection system guarantees product quality.
Resource integration capability: Ability to quickly integrate resources such as fabrics, accessories, and processes.
The production process of clothing manufacturers seems cumbersome, but every link is crucial and is related to the quality of the finished product and the brand image. From demand communication, proofing, fabric procurement, to mass production, post-processing, and delivery, every step requires excellence in order to perfectly present the customer's design concept.
For brands and entrepreneurs, understanding the production process of clothing manufacturers can not only better communicate with manufacturers, but also avoid common problems in production, improve efficiency and product quality. Choosing a reliable clothing manufacturer and actively participating in every link is the key to creating high-quality clothing products.
As a professional custom clothing manufacturer, we not only have a complete production process and advanced equipment, but also have an experienced technical team that can efficiently mass-produce clothing products with complex processes and strict requirements. At the same time, we also provide customers with flexible small-batch production services to meet the needs of start-up brands, niche customization and market testing, helping customers control costs and quickly respond to market changes while ensuring quality.
www.ncnewspring.com
ncnewspring