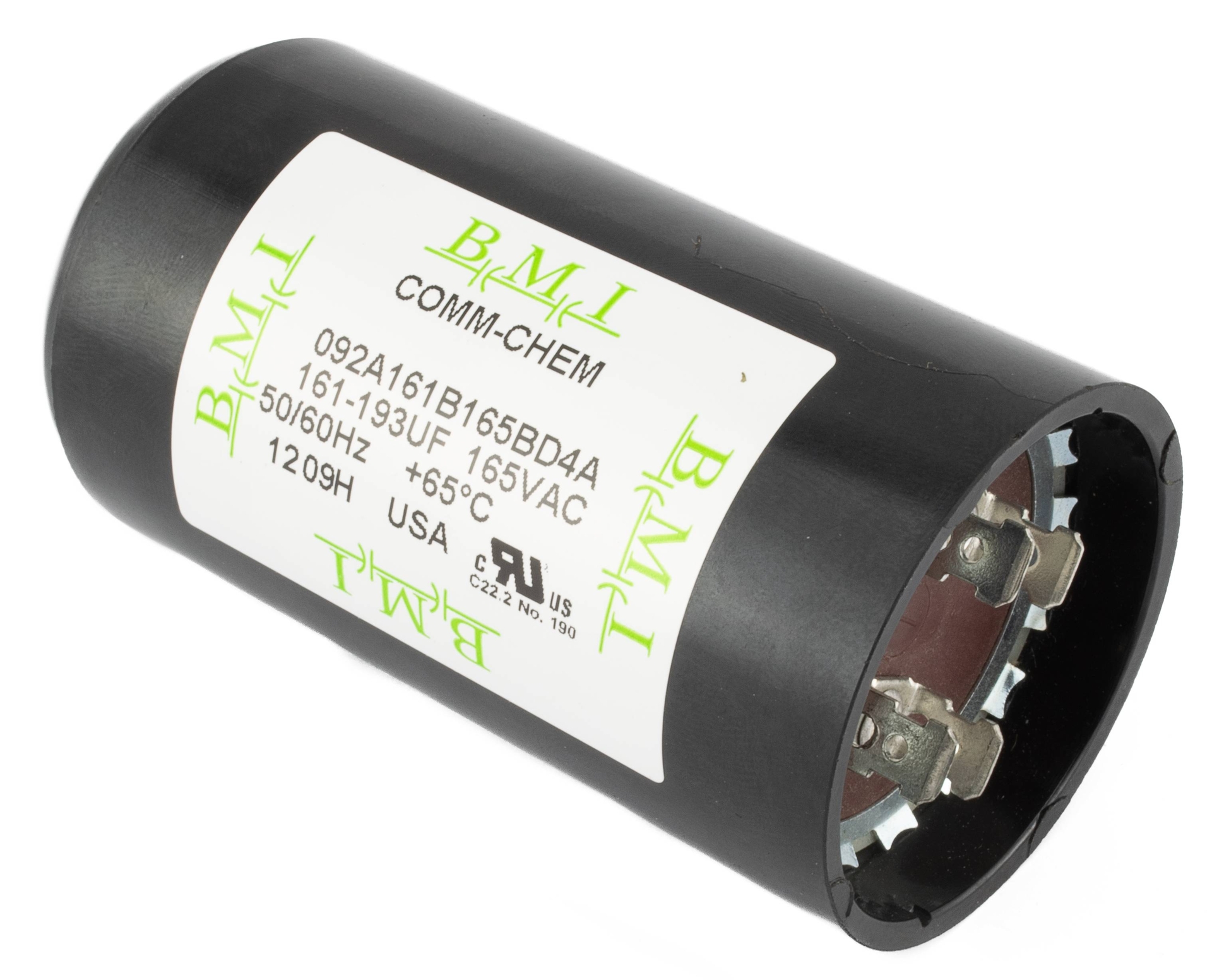
DC motors are widely used in various industries, ranging from robotics and automation to automotive and aerospace applications. These motors rely on a combination of electrical and mechanical components to convert electrical energy into mechanical motion. One crucial component that plays a significant role in the operation of DC motors is capacitors. In this article, we will delve into the reasons why DC motors have capacitors and explore their importance in enhancing motor performance and efficiency.
- Starting Torque and Speed Control:
Capacitors are commonly used in DC motors to improve their starting torque and speed control capabilities. When a DC motor is initially powered on, it requires a higher starting torque to overcome inertia and initiate motion. Capacitors connected in parallel with the motor provide an additional current boost during startup, enabling the motor to generate higher torque and accelerate more rapidly. This feature is particularly beneficial in applications where quick and precise motor response is essential, such as robotics and industrial machinery. - Power Factor Correction:
Another significant advantage of capacitors in DC motors is power factor correction. Power factor is a measure of how effectively electrical power is utilized in a system. Inefficient power factor can result in increased power consumption, reduced motor efficiency, and unnecessary strain on the power supply. By incorporating capacitors, DC motors can compensate for reactive power, leading to improved power factor and reduced energy consumption. This not only enhances the motor's overall efficiency but also helps to minimize electricity costs in industrial settings. - Suppression of Electrical Noise and Interference:
Capacitors in DC motors also serve as effective filters for suppressing electrical noise and interference. Motors, especially those used in sensitive electronic equipment, can generate electromagnetic interference (EMI) and radio frequency interference (RFI) during operation. These interferences can disrupt the performance of nearby electronic devices and cause signal degradation. Capacitors connected across the motor terminals act as low-pass filters, attenuating high-frequency noise and ensuring cleaner power supply to the motor. This feature is crucial in applications where precise control and signal integrity are paramount, such as medical equipment and communication systems. - Commutation Improvement:
Commutation is the process by which the direction of current flow in the motor's armature windings is switched, allowing continuous rotation. Capacitors play a vital role in improving commutation by reducing arcing and sparking at the motor's brushes. By connecting capacitors across the brushes, the energy stored in the capacitors helps to suppress the arcing that occurs when the brushes make contact with the commutator segments. This not only prolongs the lifespan of the brushes but also reduces electrical noise and improves overall motor performance.
Conclusion:
In summary, capacitors play a crucial role in enhancing the performance and efficiency of DC motors. From improving starting torque and speed control to power factor correction and noise suppression, capacitors offer a range of benefits that optimize motor operation. By understanding the significance of capacitors in DC motors, engineers and designers can make informed decisions to maximize motor performance in various applications. Embracing the power of capacitors is key to unlocking the full potential of DC motors in today's technologically advanced world.