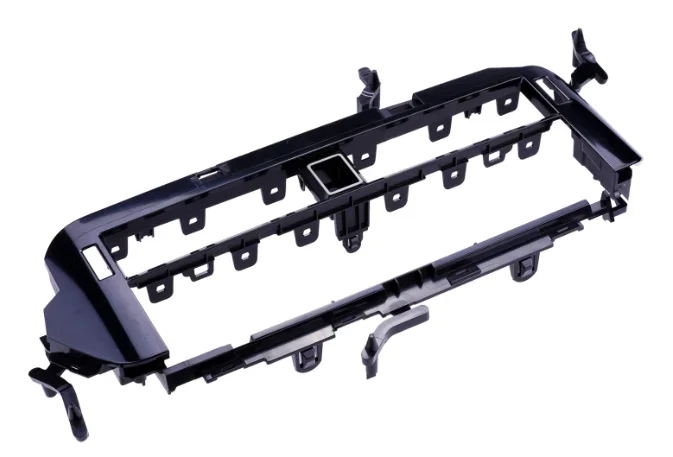
One of the most critical yet often overlooked components of a car's design is the interior. The dashboard, center console, door panels, and other interior elements are not only aesthetically important but also play a crucial role in the functionality and safety of the vehicle. This is where injection plastic mold design and manufacturing come into play, a process that is integral to the creation of these intricate parts.
Understanding Injection Molding
Before diving into the specifics of automotive interior mold design and manufacturing, it's essential to understand the basics of injection molding. This process involves injecting molten plastic material into a mold cavity, where it cools and hardens to take the shape of the cavity. The mold is then opened, and the now solid part is ejected.
The Role of Plastics in Automotive Interiors
Plastic materials are chosen for automotive interiors due to their versatility, cost-effectiveness, and ability to be molded into complex shapes. They are also lighter than traditional materials like metal, which can contribute to a vehicle's fuel efficiency. Some of the common plastics used include:
- Polypropylene (PP)
- ABS (Acrylonitrile Butadiene Styrene)
- Polyethylene (PE)
- Polycarbonate (PC)
- Polyamides (PA)
Automotive Interior Injection Plastic Mold Design
Designing an injection mold for automotive interiors is a complex process that requires a deep understanding of both the material properties and the end-use requirements of the part. Here are some key considerations:
1. Material Selection: The choice of plastic can affect the mold design, as different materials have different flow characteristics and cooling times.
2. Part Design: The part's geometry must be conducive to the injection molding process. Features like ribs, bosses, and complex undercuts can add to the complexity of the mold.
3. Gating and Runner System: The gates are the entry points for the molten plastic into the mold. The design of the gating system affects the quality of the final part, including the presence of defects like knit lines and flow marks.
4. Cooling System: Efficient cooling is crucial for the cycle time of the mold. The cooling channels must be strategically placed to ensure uniform cooling of the part.
5. Ejection System: The mold must include an effective ejection system that allows for the easy removal of the part without causing damage.
6. Tooling Material: The choice of material for the mold itself is critical. It must be able to withstand the high pressures and temperatures involved in the injection molding process.
Automotive Interior Injection Plastic Mold Manufacturing Process
Once the mold design is finalized, the manufacturing process begins. Here's a step-by-step overview:
1. CNC Machining: Computer Numerical Control (CNC) machining is used to create the precise dimensions of the mold cavities and cores.
2. Electro Discharge Machining (EDM): EDM is employed for creating intricate details and features that are difficult to achieve through traditional machining.
3. Polishing: The mold surfaces are polished to a high degree of smoothness, which is essential for the quality of the surface finish on the molded part.
4. Assembly: The various components of the mold, including the cavities, cores, and cooling channels, are assembled into a complete mold unit.
5. Testing: The mold is tested with the chosen plastic material to ensure it functions correctly and produces parts without defects.
Quality Control and Assurance
Quality is paramount in the automotive industry, where safety and performance are critical. Mold manufacturers employ various quality control measures:
1. Dimensional Verification: Ensuring that the mold's dimensions match the design specifications.
2. Surface Finish Inspection: The mold's surface finish is inspected to meet the required standards.
3. Functionality Testing: The mold is tested for its ability to produce parts with the desired features and without defects.
4. Durability Testing: The mold must be able to withstand a high number of cycles without degrading in performance.
Conclusion
The design and manufacturing of injection plastic molds for automotive interiors is a complex and highly specialized field. It requires a deep understanding of materials, design principles, and manufacturing processes. As the automotive industry continues to push the boundaries of innovation, the role of mold design and manufacturing will remain central to the creation of the safe, efficient, and stylish vehicles of the future.
Automotive Interior Injection Plastic Mold Manufacturer - Xuzhong
Xuzhong has an experienced design team and professional manufacturing technology, and has rich OEM/ODM experience in professional design and manufacturing of plastic molds, hardware molds, inserts, fixtures, etc. One-stop service from plastic mold design, mold opening, injection molding, automatic spraying, silk screen printing, pad printing finished product assembly, etc. Welcome to contact us!
https://www.xuzhongmold.com/Automotive-Interior-Injection-Plastic-Mold-Design-and-Manufacturing.html
Xuzhong
jy_dbls@xzkj-mould.com